Back in April, tQ’s Lauren Martin visited GZ Media in the Czech Republic to see how the manufacturing plant handles the increasing demand for vinyl records. While GZ Media pressed 13.7 million records last year, at the opposite end of the scale lathe cutting operations like Phil Macy’s 3.45RPM turn out one disc at a time. Instead of the rapid industrial process of pressing records from a metal master stamper, lathe cutting involves etching each record by hand in real time, a diamond stylus carving its spiral groove through warm, blank plastic.
One half of psychedelic duo Southall Riot, Phil previously helmed Victory Garden Records (and its Sides Of Unequal Length cassette offshoot) with musical partner Stuart Thompson. From 1998 to 2010, Victory Garden released several virtually unplayable oddities (lengths of master tape by Kirk Lake and Roy Montgomery, 8-track cartridges from Lughnasa/Ansuz Lúnasa, a mummified Dreams Of Tall Buildings cassette) alongside early material by Hey Colossus, One More Grain, The Lowland Hundred and Hot Chip. (“Yeah, when they were really making it big I had about 200 copies,” admits Phil of the latter, “All these bloomin’ really limited CDs hanging around under my bed collecting dust. People were going, ‘Oh it must be really rare’ but it’s not. You come and see how rare they are, I’m using them as coasters.”)
A compulsive record collector and dealer, Phil counts New Zealand’s Flying Nun label among his obsessions, and it was lathe releases on The Dead C guitarist Bruce Russell’s Xpressway and Corpus Hermeticum labels that stirred his interest in the process. In 1998, he got in touch with the man responsible, lathe pioneer Pete King, to cut 37 albums by his then-band Kashmir Twist. Before our interview in his Seaford home begins, we squeeze into Phil’s spare room for a cutting demonstration.
Phil’s lathe, a German T-560 model, has been clamped permanently in place above a Technics 1210 deck. Picking out a blank 7” disc, Phil wipes it with anti-static spray, then places it on the turntable, bolting it down with centre weights to prevent slippage. Twin lamps heat the plastic to an optimum cutting temperature before the lathe’s diamond stylus is lowered onto the rotating disc, the music to be cut (in this case, a track by The Memory Band from a forthcoming single on Static Caravan) played in externally from a CD-R.
The 1210’s own needle is introduced to the developing groove, playing back the track through the speakers a fraction of a second behind the cutting needle, so Phil can monitor the music being carved into the disc. Passing smoothly along a metal rod above the turntable, the cutting needle works its way steadily towards the centre of the disc until the music finishes, Phil stopping its movement briefly at the close to create the final locked groove. The needles are lifted, the lamps turned off and the disc is allowed to cool for a few seconds before the weights are removed. It’s prised off the deck and placed in its sleeve (or flipped if cutting a B-side).
Downstairs, Phil plays the finished disc a final time on a second Technics deck in his lounge, checking its sound quality before sticking on a centre label and presenting it to The Quietus (“I better tell Static Caravan I’ve done that”). It’s a laborious process and one that means Phil limits his cuts to a maximum of 100 7”s or 50 LPs (anyone requiring a higher quantity, he reasons, will be adequately served by traditional pressing plants).
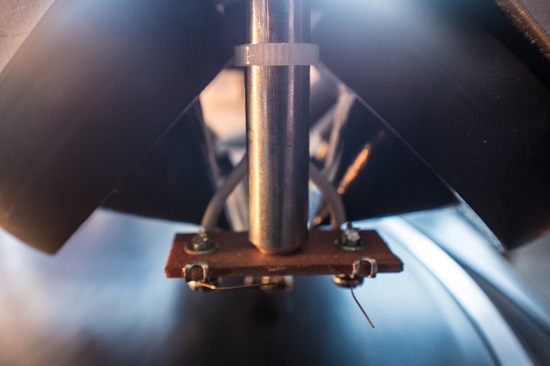
How did you get hold of your lathe cutting gear?
Phil Macy: There’s a guy in Germany, Ulrich ‘Souri’ Sourissen, who custom makes these lathes. You can’t buy one off the shelf, you have to contact him and hope he gets back to you. He’s very cautious and very reticent, you have to convince him that you’re worthy of having one of his machines. It took us about six or seven months from when I first emailed him saying, look, I’ve got the money (around 3200 Euros), I want to buy one, to actually going over there. He has to train you. I went to Germany and did 15 hours in one day, learning how to use it. And then, when he’s met you, when he knows that you’re going to be reasonably competent with it, he’ll sell it to you.
Why did you buy it?
PM: The idea came to me because I wanted to do my own stuff, very cheaply and with very small runs. I was approaching my 45th birthday and had the idea to release 45, 45RPM singles, in maximum editions of 45 copies, over the course of a year. The 454545 project will end on the 18th of Feb next year, when I’m 46. If you want to do 45 editions of 20 or something you can’t just send off to a conventional plant and get it done quickly and easily.
Did you already know people who’d want to use your service?
PM: Oh absolutely, it was a done deal. As long as I was vaguely competent at using it I was always going to have Static Caravan, Dom Earworm from Great Pop Supplement and Polytechnic Youth, Fruits De Mer, Enraptured. I knew I was going to get money for it.
Is the 454545 project on schedule?
PM: It is, I’m bang on. It’s one every eight days for a year and in the first 80 days I’ve done ten. The very first release was a Southall Riot one, ‘Encyclopedia Astronautica’, which was a two track jam we did. Southall Riot actually sells best out of the 454545 things so I’ll certainly be knocking out a few more of them. I’m doing a few collaborations with people, hopefully The Lowland Hundred, one with Dreams Of Tall Buildings, one with one of the guys out of Air Formation called ‘I Am Your Captain’, remixes or whatever. But I have hundreds and hundreds of hours on tape to choose from.
What about other people’s music?
PM: The lathe came back at the end of September and I started cutting pretty much instantly. I did the first cut for Static Caravan, a Pete Philipson 10”, in the first week of October and since then I’ve done about 1,000 commercial cuts. There’s still a hell of a lot I need to learn. If you don’t get the treble and the bass right then you put a lot of stress on the needle. Bass makes it go side to side and treble makes it go up and down, so what you’re trying to do is get an ideal balance where it’s going along as smoothly as possible. If you have too much bass you can ruin a needle ‘cos it’s popping out of the groove and ruining the cuts.
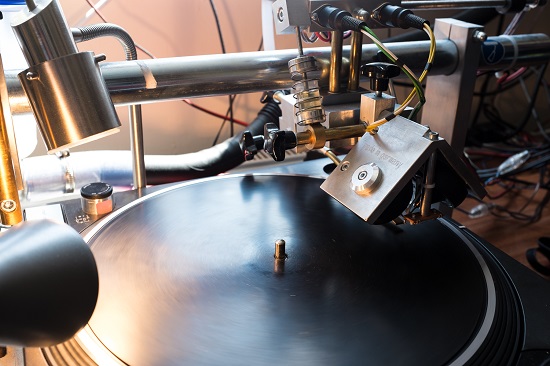
How do lathe discs compare with standard vinyl, dubplates and acetates?
PM: The actual quality of the plastic varies. I get mine direct from Souri and he sources plastic which he knows works with his machine. Technically speaking it isn’t vinyl but if you want to look at that and tell me that doesn’t look like vinyl… to all intents and purposes let’s call it vinyl. That record you have there, play it 50 times and if you have a nice needle and you treat it right there shouldn’t be any deterioration in quality. A lot of dubplates use much softer plastic, which will deteriorate after ten plays or something. Saying that, there’s all sorts of places you can get plastic from so I don’t want other lathe cutters knocking on my door, saying I’m dissing them. Acetates, that’s just the metal plate with a lacquer on top, they were always just for test listening, three or four times. They were done for bands to have a demo – before you had cassette tapes, you’d get it cut on a lacquer. Send it to the board room and EMI would say (affects plummy, George Martin voice) “Oh that sounds good!” and then you’d press up the whole thing. Or not.
Is there much competition in lathe cutting?
PM: I know other people who have machines but not many appear to be offering them out to the public. I guess there are perhaps 30 in the country but maybe at the maximum there’s six or seven in constant public usage. I am surprised more people don’t do it, even just for projects on a personal basis. I bought this really to cut my own music but obviously you’re going to make money cutting other people’s stuff, that’s a no-brainer.
How does having a lathe cutter fit in with the current vinyl resurgence?
PM: All this record boom, it made no difference at all to whether I was going to get a lathe or not. There will always be people out there who want their stuff on vinyl. That was never going to die. People saying, “Oh vinyl’s dead.” No. People wanting One Direction picture discs, people wanting a 200 gram Fleetwood Mac copy of Rumours, that doesn’t affect me. I bought the lathe because I wanted to make stuff, I can do more Victory Garden stuff if we want or I can do something else. It’s the Marxist thing of owning the means of production. Once you own the means of production, once you own the factory, you basically have the whole thing. It’s almost anarcho-syndicalist. You don’t have any bosses. If I don’t want to cut something, I won’t cut something. I don’t have to take other people’s money. You’re your own little commune of self-productivity. You don’t get swallowed up.